本帖最后由 seven_nana 于 2017-6-22 18:58 编辑
摘要
日本海军舰船所用的重型装甲都是在吴海军工厂(位于广岛县的吴市)或北海道的室兰市(即日本制钢所)制造的。吴海军工厂能够生产所有类型与规格的装甲,且具备大规模生产能力,而室兰工厂的产能只有吴海军工厂的30%,且只能制造8英寸以下厚度的均质装甲。室兰工厂所采用的制造工序与吴海军工厂基本一致,仅在部分细节上结合本地情况进行了调整。
负责重型装甲的实验与开发工作的则有数个不同的机构,其中最主要的是目黑的海军第二研究所、仙台的金属材料研究所、以及包括实验室、兵工厂、测试场等在内的吴市海军机构。前两处机构主要负责基础研究与缩小比例实验,而后者则负责全比例实验,并对生产方面存在的障碍进行研究。
装甲板类型
日本海军重型装甲板的分类情况如下:
均质装甲
NVNC | New Vickers Non-Cemented | 新维克斯均质装甲 | MNC | Molybdenum Non-Cemented | 含钼合金钢均质装甲 | CNC | Copper Non-Cemented | 含铜合金钢均质装甲(此外还有CNC1与CNC2这两种变体) |
表面硬化装甲
VC | Vickers Cemented | 维克斯渗碳装甲 | VH | Vickers Hardened | 维克斯硬化装甲 |
除了上述的量产型装甲外,日本海军还研究过多种试验产品,如MNC的变体(MNC1)和表面硬化版本(MH与MH1)、CNC的变体(CNC3)和表面硬化版本(CH1)等,但这些试制版本从未投入量产过。
战舰上所配备的装甲板,其厚度最薄的约为1英寸。如需使用更薄厚度的材料以求获得部分破片防护效果,则会使用一种名为Ducol的高锰中碳钢(简称DS)。至于不直接暴露在破片杀伤范围下的结构材料,则会使用一种名为高张力钢的含镍低碳钢(简称HT)。
化学成分
以下数据均为生产规格要求
材料类型 | 碳 | 硅 | 硫 | 磷 | 锰 | 镍 | 铬 | 铜 | 钼 | NVNC | 0.43-0.53% | <0.35% | <0.035% | <0.045% | 0.30-0.45% | 3.7-4.2% | 1.8-2.2% | <0.25% | - | VC | 0.43-0.53% | <0.35% | <0.035% | <0.045% | 0.30-0.45% | 3.7-4.2% | 1.8-2.2% | <0.25% | - | VH | 0.43-0.53% | <0.35% | <0.035% | <0.045% | 0.30-0.45% | 3.7-4.2% | 1.8-2.2% | <0.25% | - | MNC | 0.30-0.38% | <0.35% | <0.035% | <0.045% | 0.30-0.45% | 3.3-3.8% | 1.8-2.3% | <0.25% | 0.25-0.40% | CNC | 0.38-0.46% | <0.35% | <0.035% | <0.045% | 0.30-0.45% | 2.5-3.0% | 0.8-1.3% | 0.9-1.3% | - | CNC1 | 0.38-0.46% | <0.35% | <0.035% | <0.045% | 0.30-0.45% | 1.8-2.3% | 1.5-2.0% | 0.6-1.0% | 0.10-0.20% | CNC2 | 0.38-0.46% | <0.35% | <0.035% | <0.045% | 0.30-0.45% | 1.3-1.8% | 1.5-2.0% | 0.6-1.0% | 0.10-0.20% |
作为对比,此处一并列出DS的化学成分(平均值)
材料类型 | 碳 | 硅 | 硫 | 磷 | 锰 | 镍 | 铬 | 铜 | 钼 | DS | 0.23-0.24% | 0.35% | <0.035% | <0.045% | 1.40% | 微量 | - | 0.20% | - |
各类日本均质装甲的镍含量与铜含量:
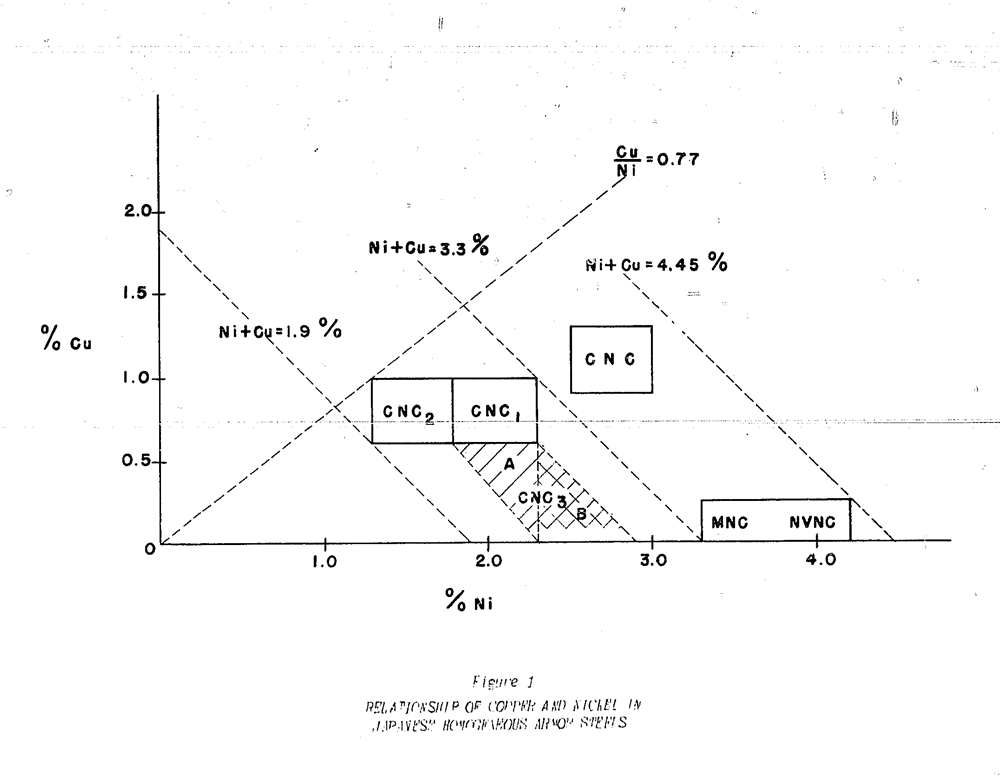
日本装甲的发展历程
1900:制成了两块150mm厚的克虏伯渗碳(KC)装甲,这是日本首次制造出真正的装甲钢。
1905:为生驹号制造了约2000吨重的KC装甲,制法即沿袭上述的试制装甲。
1910:维克斯-阿姆斯特朗公司向日本提供了大量维克斯渗碳(VC)装甲。
1915:以上述VC装甲为模仿样本,日本制成了一块200mm厚的VC装甲。
1925:制成了一块镍含量为4%的试制型NVNC。
1926:制成了一块450mm厚的试制型VC,这是当时所能制造的最厚的装甲板。
1928:试制了厚度渐减的装甲板,其目的是为了降低并更好得分配重量。
1931:为降低镍的消耗,制出了一批试制型CNC,并对1.4英寸、1.7英寸、2.5英寸、3.9英寸、8.5英寸这几种厚度的装甲进行了弹道测试。测试显示,3.9英寸及以下厚度的CNC的抗弹性能与NVNC相当,而8.5英寸的则不如NVNC。依照上述原因,并结合安全角度考虑,CNC被设定为用于75mm(3英寸)以下厚度的装甲。
1937:开发出了用于替代VC的VH装甲。在经过一系列的弹道测试考验后,日本海军出于以下几点经济方面的考量,正式采用了VH装甲:
1)渗碳过程需要消耗大量燃料,制造VH不需要
2)渗碳过程需要使用渗碳材料,制造VH不需要
3)增加车间产能
4)降低制造周期
5)有必要时,可将存在部分缺陷的装甲板轧制成较薄的NVNC
6)避免或降低硬化后表面产生龟裂的可能性
如上文表格所述,NVNC与VH的化学成分相同,其含碳量均为约0.5%,因此在制造处理过程中,是可以将VH转化为NVNC的。
采用VH替代VC并非源于抗弹性能上的考量。测试表明,在大厚度(13英寸到17英寸)级别上VH仅略优于VC;而在中小厚度级别上VH仅与VC相当,有时甚至更差(如6英寸厚度上)。
日方声称,VC与VH这两种不同类型的装甲板之间的性能差异,并不会大过两块同类型装甲板之间的差异。
请注意,日本海军仅在战列舰上使用表面硬化装甲,巡洋舰与航空母舰使用的都是均质装甲。小厚度的表面硬化装甲也有生产,但仅用于实验或弹道测试目的,其中最薄的是一块在吴海军工厂发现的100mm厚的VC,而最薄的VH则是在亀ヶ首测试场发现的,其厚度为183mm。
1940:制成了MNC。日方声称,MNC在面对大角度命中弹时具有更好的抗弹性能,且更能抵御冲击。MNC与NVNC的用途可互为替换,但主要用于水平装甲。在面对高强度冲击时,MNC发生晶体断裂的可能性低于NVNC。
1942:为了进一步降低镍的消耗,又开发出了新的CNC配方。如前文所述,此类配方不适用于大厚度装甲。新配方的目的是在维持抗弹性能的前提下进一步降低镍的消耗,其测试结果如下:
1)在4英寸以上厚度时,各类CNC配方均不理想
2)在1.4英寸、2英寸、以及3.9英寸厚度上,CNC1的抗弹性能与CNC相当
3)在1.4英寸与2英寸厚度上,CNC2的抗弹性能与CNC相当,而3.9英寸厚度上则不如CNC
4)基于以上因素考量,CNC1被设定为用于1.5英寸至3.9英寸厚度的装甲上,CNC2被设定为用于1英寸至1.5英寸厚度的装甲上,4英寸以上厚度的装甲依然采用NVNC或MNC
1943:继续针对含铜合金钢进行试验,制成了一种计划用于水平防护的材料,CNC3。由于此时的日本不仅缺镍,同时也缺铜,因此其铜含量也有所降低。CNC3的铜与镍含量合计在2.4-2.9%左右,且铜含量最大不超过0.8%(通常低于此数)。
冶炼铸锭流程
除少数以实验为目的的特例之外,所有装甲板都是使用酸性平炉冶炼的。在冶炼重型装甲板时,有时需要同时用到三个平炉才能将铸锭用的模具填满。最大型的平炉为70吨级,炼钢时使用65-70%的废料。相比多次加热铸锭,日本海军自然更倾向一次加热铸锭,原因显而易见,一次加热铸锭法得到的钢锭组织更为扎实,且需切削舍弃的部分也较少。
制造大和级战列舰所用的16.5英寸(420mm)厚度的VH装甲板时使用的大型铸锭,重量可达175吨,采用顶部浇铸模式铸锭,其截面形状为圆角矩形,大致尺寸如下:
位置 | 长度 | 宽度 | 厚度 | 钢锭头部 | 52英寸(1310mm) | 107英寸(2710mm) | 75英寸(1900mm) | 钢锭本体 | 143英寸(3625mm) | 115英寸(2860mm)/112.5英寸(2910mm) | 75英寸(1900mm) |
铸锭完成后,钢锭顶部30%以及底部10%的部分会被切削舍弃,因此实际生产出的成品装甲板的最大重量通常在100吨左右。在实际生产中,若是采用一次加热法制造装甲板时,有时会将切削舍弃的部分从40%减少到30%。
锻造轧制流程
对于成品厚度在8.7英寸(220mm)以下的装甲板,日本海军只使用轧制处理,而对于成品厚度在8.7英寸(220mm)以上的装甲板,日本海军则会先采用锻造法将铸锭厚度减半,随后再进行轧制。
制造大和级战列舰所用的16.5英寸(420mm)厚度的VH装甲板时使用的大型铸锭,经切削后重量约为100吨,其尺寸大致如下:
长度 | 宽度 | 厚度 | 85英寸(2160mm) | 112英寸(2860mm) | 75英寸(1900mm) |
完成切削后,这块铸锭所需经历的锻造轧制流程如下:
1)32小时加热至1200℃,保持10-15小时
2)通过锻压,首先将钢锭厚度从75英寸(1900mm)降低至61英寸(1550mm),随后再降低至53英寸(1350mm)
3)25小时加热至1200℃,保持8-10小时
4)通过锻压将钢锭厚度降低至43.5英寸(1100mm)
5)20小时加热至1200℃,保持8小时
6)通过轧制将钢锭厚度降低至33.5英寸(850mm),随后再降低至23.5英寸(600mm)
7)28小时加热至650℃,保持32小时,随后空气冷却,再用28小时加热至650℃,保持30小时,随后空气冷却
8)缺陷处理
9)25小时加热至1200℃,保持8小时
10)轧制成16.5×161×256英寸(420×4100×6500mm)的钢板
11)20小时加热至650℃,保持20小时,随后空气冷却
最为厚重的铸锭是由日本产的5万吨级液压机(全日本最大的液压设备)完成锻造的。轧制则是由两台9000马力级的轧钢机完成的,其中一台是由英国的戴维兄弟(Davy Bros.)公司制造的,其轧棍直径为48英寸(1220mm),长度为11英尺10英寸(3610mm),另一台则是由日方依照那台英国设备仿制而成的,其轧棍直径为48英寸(1220mm),长度为20英尺7英寸(6230mm),这两台轧钢机都是由往复式蒸汽引擎驱动的。
成品装甲的最大尺寸
长度 | 11000mm | 宽度 | 4500mm | 厚度 | 660mm | 重量 | 100吨 |
表面渗碳处理工序
新式的VH装甲并不使用表面渗透处理,然而老式的VC装甲则需要在完成锻造轧制后进行表面渗碳处理,其流程如下:
1)将两块装甲板面对面放置,装甲板之间铺上渗碳材料,并用角铁进行固定
2)渗碳材料可细分为三层,第一层是0.375-0.5英寸厚度的骨灰,第二层是2.25-2.5英寸厚度的木炭,第三层则又是0.375-0.5英寸厚度的骨灰,总厚度约为3英寸
3)将装甲板置于炉中,加热至930℃,保持2至7日(时间取决于装甲板厚度及渗碳材料质量)
渗碳工序完成后,装甲表层的碳含量能达到1.3%甚至更高。至于表面高碳含量造成的奥氏体残留问题,在日方人员眼中似乎并不是什么问题,他们似乎也并不知晓这可能带来的不良影响。
VC装甲板的表层部分碳含量:
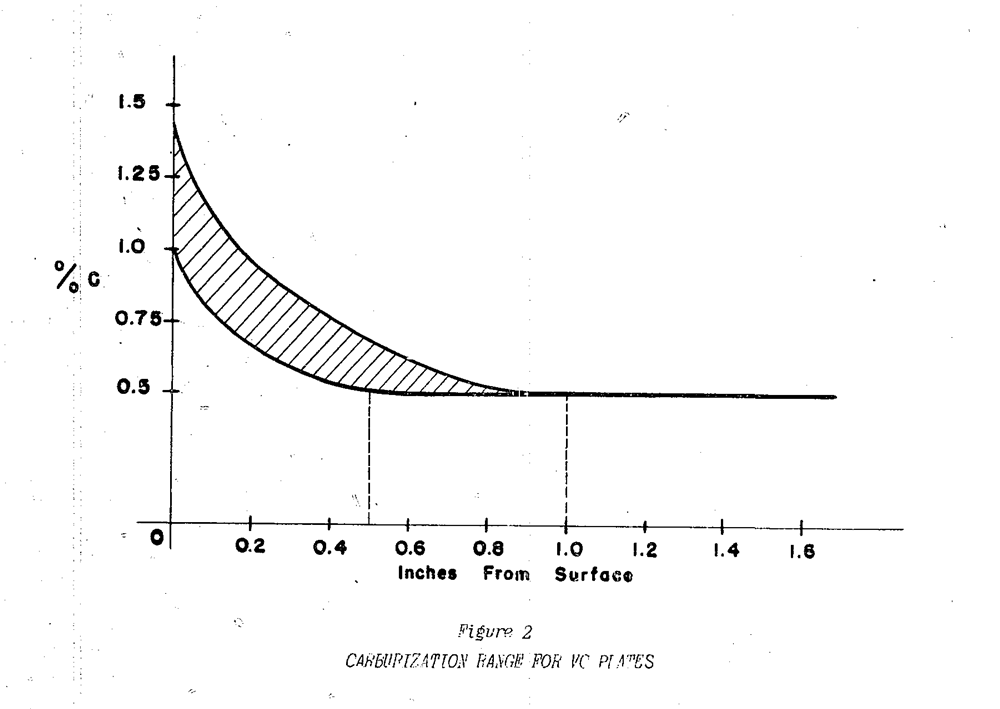
横轴表示与装甲表面之间的距离,纵轴表示该距离上的碳含量,渗碳层的深度在0.5-1英寸之间,平均值约为0.625英寸。
热处理工序
就流程工序和处理温度而言,各类均质装甲的热处理工序是大致相当的,当然了,不同厚度的装甲板所需的加热与保持时间显然是不一样的,此外在处理薄板则会省略一些工序。淬火处理时通常加热到840-860℃,回火处理时通常加热到640-670℃,进行装甲板校正时通常加热到690-700℃。热处理工序的典型例子如下:
25mm厚度
1)加热5小时,放置4小时,菜籽油淬火
2)加热6小时,放置5小时,喷水冷却
3)加热6小时,放置5小时,喷水冷却
250mm厚度
1)加热10小时,放置8小时,菜籽油淬火
2)加热12小时,放置10小时,喷水冷却
3)加热12小时,放置10小时,喷水冷却
4)加热10小时,放置8小时,菜籽油淬火
5)加热12小时,放置10小时,喷水冷却
6)加热12小时,放置10小时,喷水冷却
7)加热12小时,放置10小时,喷水冷却
420mm厚度
1)加热22小时,放置20小时,菜籽油淬火
2)加热18-20小时,放置16-18小时,喷水冷却
3)加热18-20小时,放置16-18小时,喷水冷却
4)加热22小时,放置20小时,菜籽油淬火
5)加热18-20小时,放置16-18小时,喷水冷却
6)加热18-20小时,放置16-18小时,喷水冷却
7)加热18-20小时,放置16-18小时,喷水冷却
8)加热18-20小时,放置16-18小时,喷水冷却
表面硬化处理工序
1)将装甲板放置在厚度与其大致相当的湿沙上,装甲板与湿沙的四周包裹有防火砖,湿沙下方则垫有2块3-4英寸厚度的钢板
2)在装甲板上进行钻孔,深度约为装甲板厚度的70%,随后在装甲板表面以及钻出的孔中各放置一个热电偶。
3)使用发生炉煤气,将西门子反射炉预加热至1100-1150℃
4)将装甲板放入西门子反射炉,并进行迅速加温,直至钻孔中的温度达到730℃,此时装甲表面温度至少应已达到850℃
5)将装甲板取出反射炉,随后对正反面进行喷水冷却
硬化处理完毕的VH与VC装甲的硬度分布对比曲线:
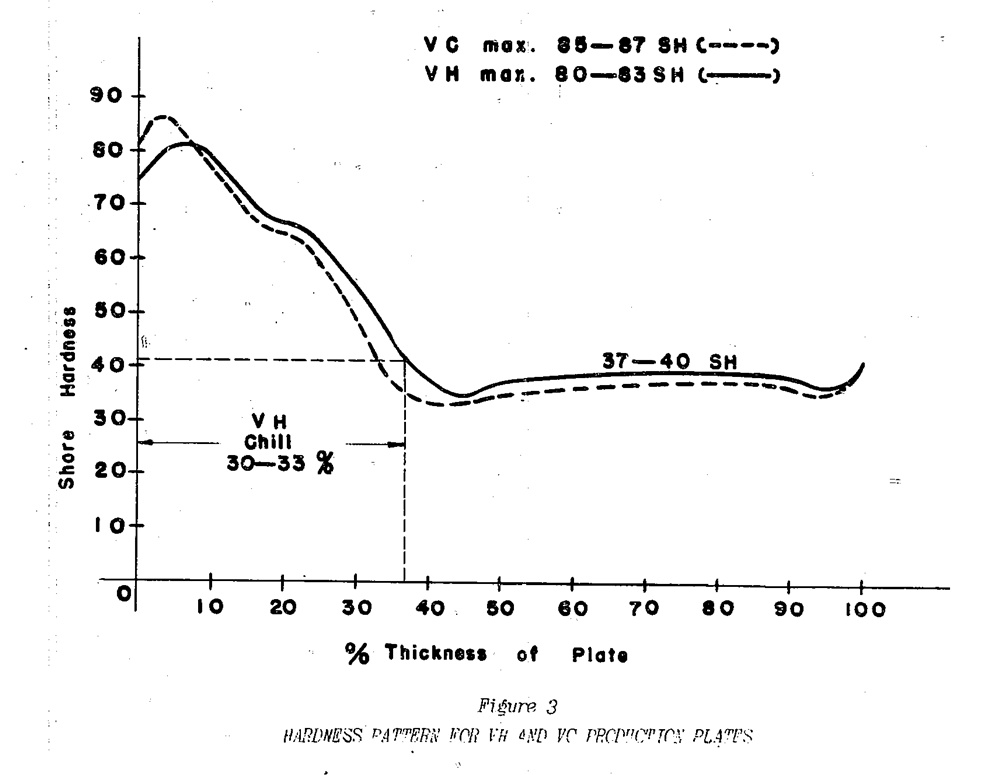
日本海军以肖氏硬度42作为硬化层分界线,VH装甲的理想硬化深度应在30-33%左右,但部分试制型装甲板的硬化层深度则达到了40%。
在完成硬化工序后,日本海军并不会对其进行应力消除处理,不过在战争开始之前的日子里,制造完毕的装甲板会先放置6个月以检验其是否会在普通环境下产生裂纹,随后才会送入造船厂。
机械性能测试
材料类型 | 厚度 | 屈服点(kg/mm²) | 抗拉强度(kg/mm²) | 伸长率(%) | 断面收缩率(%) | 悬臂梁冲击强度(ft/lb),平均值 | 悬臂梁冲击强度(ft/lb),最小值 | NVNC | <75mm | >50 | 85±5 | >18 | >40 | >30 | >25 | 75-180mm | >45 | 80±6 | >19 | >40 | >33 | >28 | >180mm | >40 | 75±7 | >20 | >40 | >35 | >30 | VC | 75-180mm | >45 | 80±6 | >19 | >40 | >33 | >28 | >180mm | >40 | 75±7 | >20 | >40 | >35 | >30 | VH | 75-180mm | >45 | 80±6 | >19 | >40 | >33 | >28 | >180mm | >40 | 75±7 | >20 | >40 | >35 | >30 | MNC | 75-180mm | >50 | 85±5 | >20 | >40 | >35 | >30 | >180mm | >40 | 75±7 | >21 | >40 | >40 | >35 | CNC | <75mm | >60 | 85±5 | >19 | >40 | >30 | >25 |
悬臂梁冲击强度是常规的冲击测试,测试环境是在低温环境(最低40℃)下进行的。日方人员称,对于普通的量产型装甲板而言,即便测试时的温度下降至-40℃,冲击测试结果也不会出现明显的下降。且日方人员还声称,只要冲击强度不小于30ft/lb,则装甲板的抗弹性能与冲击强度无关,然而当冲击强度低于30ft/lb时,则装甲板的抗弹性能将会低于平均水准。
成品装甲板的尺寸重量误差允许范围
厚度误差(平均值):
厚度 | 允许误差范围 | <100mm | +0mm,-2mm | 100-250mm | +0mm,-4mm | >250mm | +2mm,-4mm |
厚度误差(局部值):
厚度 | 允许误差范围 | <100mm | +2mm,-3mm | 100-250mm | +3mm,-6mm | 250-400mm | +3mm,-10mm | >400mm | +3mm,-14mm |
重量误差:
厚度 | 允许误差范围 | <100mm | +0kg/m²,-20kg/m² | >100mm | +0kg/m²,-25kg/m² |
弹道性能测试
Vd = 1530×(D^0.75×T^0.7)/P^0.5
D = 炮弹弹径(单位为dm)
T = 装甲厚度(单位为dm)
P = 炮弹重量(单位为kg)
日方使用的德玛尔公式中并没有角度修正值,且原是用于估测老式穿甲弹在0度入射角下的穿甲能力的,因此无法直接估测91式穿甲弹的穿甲能力,故需要经过质量系数(Figure of Merit)的修正。修正后的速度即为弹道极限,其衡量标准与美国类似(弹体大部分穿过装甲板,且剩余速度为0)。
以下数值乃是20.3cm穿甲弹在各个角度下射击均质装甲时的质量系数(此处并未考虑T/D比值发生变化时质量系数的变化情况):
炮弹类型 | 装甲类型 | 测试角度 | 质量系数 | 20.3cm 91式穿甲弹 | NVNC/MNC | 0° | 1.30 | 10° | 1.30 | 20° | 1.32 | 30° | 1.37 | 40° | 1.48 | 50° | 1.72 | 55° | 1.92 | 60° | 2.17 | 65° | 2.49 | 70° | 2.91 |
装甲板的验收测试
对装甲板进行验收测试时,使用的质量系数与上述数据有所不同(因为考量方式不同,详见下文)。
测试之前会首先测量装甲板的厚度,此处厚度指装甲板四个角落的厚度的平均值。
测试时所用的炮弹不装炸药,改为装填沙子,其重量与装药量相当。
测试装甲板时所发射的炮弹数量不超过三发,第一发炮弹射击装甲板靠近底部角落处,第二发炮弹射击装甲板顶部靠近角落处,第三发则向任何合适的位置射击。
测试用于垂直防护的装甲板时,炮弹落点与装甲板边缘之间的距离至少应在3倍弹径以上,且每一发炮弹之间的落点也至少应在3倍弹径以上;而测试用于水平防护的装甲板时,炮弹落点与装甲板边缘之间的距离至少应在4倍弹径以上,每一发炮弹之间的落点则视装甲板的崩落情况而定。
以下内容是各类条件的测试规格(质量系数是我计算的):
垂直防护装甲
炮弹类型 | 装甲类型 | 装甲厚度 | 测试角度 | 测试速度 | 质量系数 | 46cm 91式穿甲弹 | VH/VC | >400mm | 30° | ? | ? |
由于保密的缘故,46cm穿甲弹的测试规格不明。
炮弹类型 | 装甲类型 | 装甲厚度 | 测试角度 | 测试速度 | 质量系数 | 41cm 91式穿甲弹 | VH/VC | 400mm | 20° | 395m/s | 1.084 | 375mm | 375m/s | 1.077 | 350mm | 355m/s | 1.070 | 325mm | 335m/s | 1.064 |
炮弹类型 | 装甲类型 | 装甲厚度 | 测试角度 | 测试速度 | 质量系数 | 36cm 91式穿甲弹 | VH/VC | 325mm | 20° | 385m/s | 1.105 | 300mm | 360m/s | 1.093 | 275mm | 335m/s | 1.081 | 250mm | 310m/s | 1.069 |
炮弹类型 | 装甲类型 | 装甲厚度 | 测试角度 | 测试速度 | 质量系数 | 20.3cm 91式穿甲弹 | NVNC/MNC | 150mm | 20° | 355m/s | 1.151 | 125mm | 305m/s | 1.124 | 100mm | 260m/s | 1.120 |
炮弹类型 | 装甲类型 | 装甲厚度 | 测试角度 | 测试速度 | 质量系数 | 15.5cm 91式穿甲弹 | NVNC/CNC | 100mm | 20° | 315m/s | 1.108 | 75mm | 265m/s | 1.140 |
在上述测试条件下,若是炮弹的定心带之后的部分未能穿入装甲板,则可认为这块装甲板通过了验收测试。
水平防护装甲
炮弹类型 | 装甲类型 | 装甲厚度 | 测试角度 | 测试速度 | 质量系数 | 46cm 91式穿甲弹 | NVNC/MNC | >200mm | 55° | ? | ? |
由于保密的缘故,46cm穿甲弹的测试规格不明。
炮弹类型 | 装甲类型 | 装甲厚度 | 测试角度 | 测试速度 | 质量系数 | 41cm 91式穿甲弹 | NVNC/MNC | 200mm | 55° | 400m/s | 1.784 | 175mm | 360m/s | 1.763 | 150mm | 315m/s | 1.718 |
炮弹类型 | 装甲类型 | 装甲厚度 | 测试角度 | 测试速度 | 质量系数 | 36cm 91式穿甲弹 | NVNC/MNC | 150mm | 55° | 365m/s | 1.800 | 125mm | 315m/s | 1.765 | 100mm | 265m/s | 1.736 |
炮弹类型 | 装甲类型 | 装甲厚度 | 测试角度 | 测试速度 | 质量系数 | 20.3cm 91式穿甲弹 | NVNC/CNC | 100mm | 55° | 405m/s | 1.745 | 75mm | 320m/s | 1.686 | 60mm | 230m/s | 1.417 |
炮弹类型 | 装甲类型 | 装甲厚度 | 测试角度 | 测试速度 | 质量系数 | 15.5cm 91式穿甲弹 | NVNC/CNC | 75mm | 55° | 415m/s | 1.745 | 60mm | 290m/s | 1.458 | 50mm | 230m/s | 1.314 | 50mm | 65° | 330m/s | 1.885 | 35mm | 250m/s | 1.833 |
在上述测试条件下,若是炮弹未能完整穿透装甲板(允许有碎块穿过装甲板),则可认为这块装甲板通过了测试。
当装甲板通过了测试规格考验时,后续炮弹会以更高的速度进行射击,以了解这块装甲板的真实性能。
亀ヶ首测试场上的一个典型的测试用靶跺:
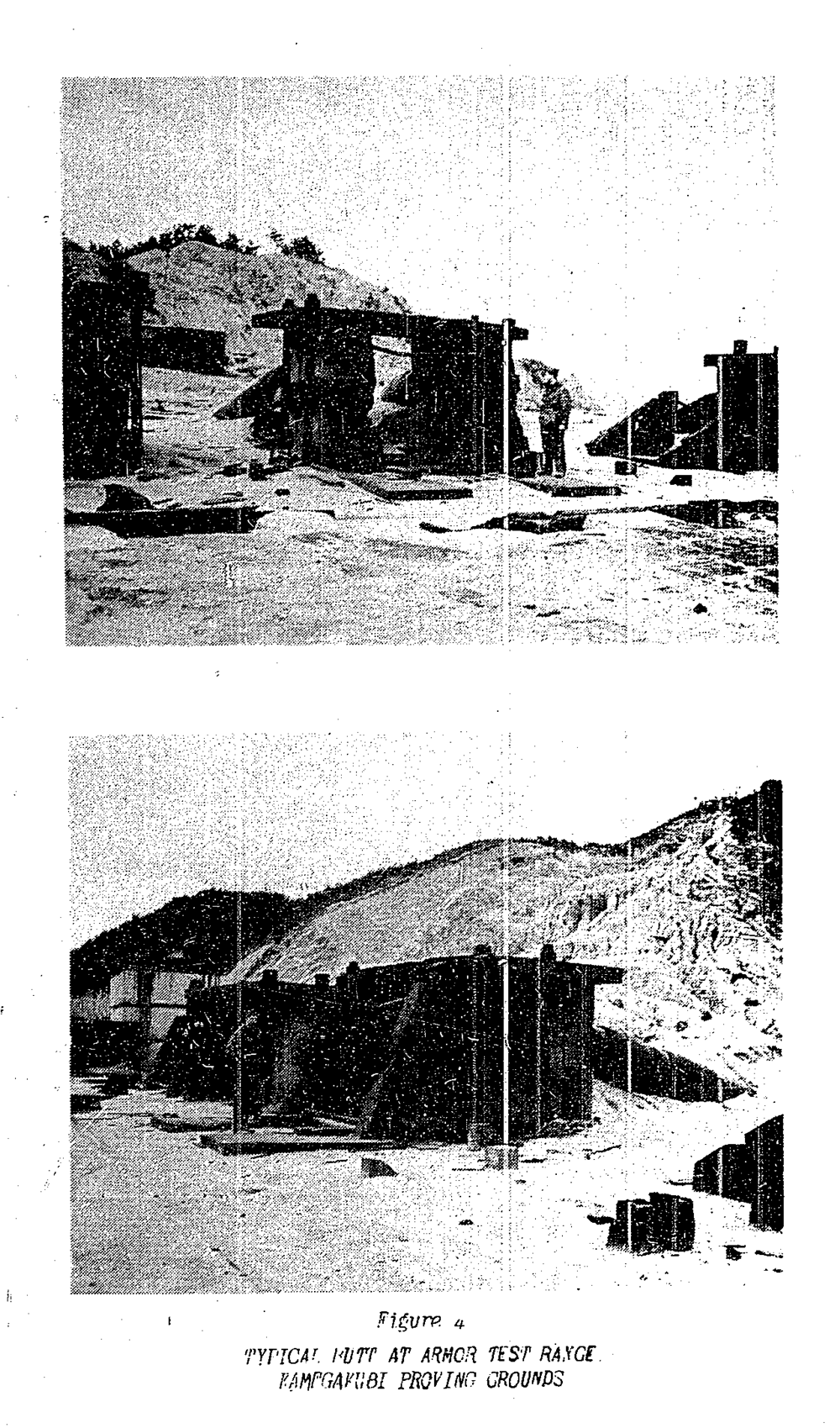 |